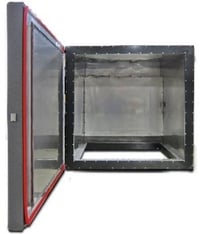
MIL-AERO Thermal Management & Test Systems
These thermal systems provide precision temperature control for MIL-AERO component characterization, testing, and production:
Thermal Environment & Active Heat Sink Simulation
Two thermal plates are integrated with a chamber each with independent control of temperature. The plates provide active heat sinking as the chamber simulates the harsh temperature environments of space.
Touch-screen temperature controls with remote communications capabilities provide a common platform across all thermal chamber and plate systems.
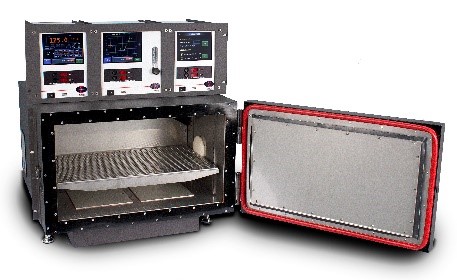
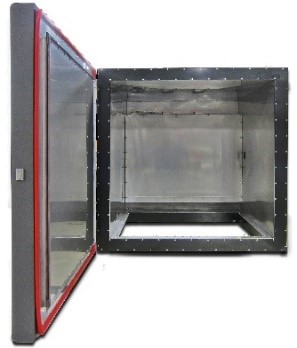
Aircraft Landing Gear Thermal Stress Testing
A cryogenic thermal test chamber integrates with a vibration table for aircraft landing gear development and production. The 30x30x30” chamber was specified for aggressive transition rates (>35°C per minute HOT and >15°C per minute COLD).
Optimizing chamber size to accommodate the vibration table and landing gear geometry with precise control of a liquid nitrogen source, provided fast transition rates over its specified temperature range.
RF Component Vacuum Thermal Test
Integrating a large surface (384 sq.in., 2,477 sq cm) thermal plate with vacuum bell jar provided a system for production test of RF satellite communications products without the need for a vacuum chamber.
The thermal system delivered a temperature range of -65 to 200°C.
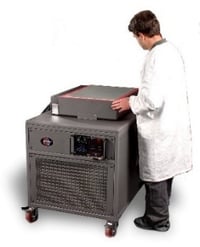
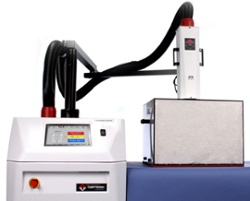
Characterizing RF Components
Temperature characterization of RF (Wifi, Bluetooth) components is a challenge when low signal attenuation is the goal. A poly-carbonate exterior and white glass interior chamber did the job.
The hood-style RF chamber uses a portable ThermoStream air forcing system as the temperature source for rapid (up to 15°C/sec) and accurate thermal cycling.
Avionics Thermal Management Simulation
This application required a small footprint, bench-top system delivering continuous high volume (6 to 43scfm), low pressure, temperature-controlled air. Thermal cycling was between 20 and 70°C with accuracy at ±1.0°C
A broad family of forced convection temperature systems, using only compressed air, provide thermal cycling from -100 to +300°C.
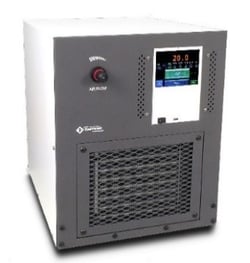
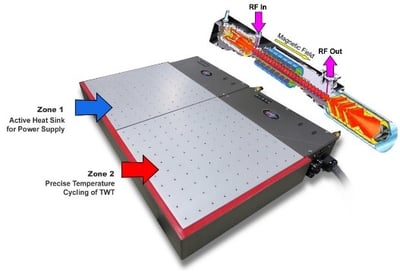
Thermal Plate for Satellite Component Testing
This 2-zone temperature plate provided simulation of space-borne temperature extremes while serving as an active heat sink for high-heat dissipation devices. Multiple plate systems were used for production tuning of satellite components.
Surface dimensions and hole-patterns were designed to accommodate and secure the unit under test.
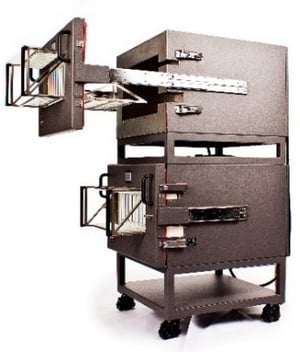
Military Electronic Component Design and Production
Testing multiple board-level products to JDEC and IPC standards can require many temperature cycles over a wide range. This cryo chamber is configured with connectors on both sides of its sliding doors for easy access and fast set up of multiple load and test boards.
Stacked chambers save floor space by doubling capacity in the same space as a single chamber.