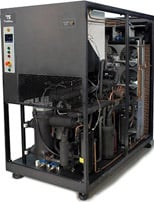
Absolute Zero
Absolute zero is the bottom limit of the thermodynamic temperature scale. It is the point at which all thermal motion ceases; a state at which the enthalpy and entropy of a cooled ideal gas reach their minimum values. At this point, the fundamental particles of nature have minimal vibrational motion, retaining only quantum mechanical particle motion. It is the zero point on the Kelvin scale (-273.15°C or -459.67°F)
Actuator
An actuator is the component of a system that is responsible for moving or controlling a mechanism in that system. Actuators uses a control signal (electric current, computer command, pneumatic or hydraulic pressure, human power) and a source of energy (electric current, hydraulic or pneumatic pressure). When the control signal is received, the actuator responds by converting that energy into mechanical motion. Air-Cooled Chiller Air Cooled Chillers use Ambient Air to remove heat from the system; typically using Fans or CDA (Clean Dry Air) streams to pass air over Condenser Coils; removing heat from the condensing Refrigerant and rejecting the Heat to the surrounding atmosphere. Generally used for small to medium applications requiring two hundred tons of cooling or less.
Ambient Temperature Range
Ambient Temperature is the Temperature of the Environment that surrounds, or is outside of the Process/Cooling Medium. Standard Ambient Temperature is generally considered to be 25 °C, (77 °F/298.15 K) at an absolute pressure of 1 atm.
ANSI
The American National Standards Institute (ANSI) is a private non-profit organization that oversees the development of voluntary consensus standards for products, services, processes, and systems in the United States. The organization also coordinates U.S. standards with International standards so that American products can be consumed worldwide. ANSI accredits standards that are developed by representatives of other standards organizations, many of which, whose standards are applicable to the design, manufacture and documentation of state-of-the-art Chiller Equipment, are discussed in this Glossary.
Argon
Argon is an inert gas naturally found in the atmosphere, and easily produced as a byproduct of cryogenic air separation. In the Chiller Industry, Argon is used as a Heat Transfer Medium in Gas Chillers.
Boiling Point
Boiling Point is the temperature at which a liquid (here, Heat Transfer Fluid and Refrigerant) begins to change from a liquid to a gaseous state, or boils. It is necessary to choose fluids, and design and program Chiller Systems, such that the fluids in the sytem do not reach the boiling point.
BTU
The British thermal unit (BTU) is a traditional unit of work equal to about 1055 joules. It represents the amount of work needed to raise the temperature of one pound of water by one degree Fahrenheit. In the Chiller Industry. The BTU is often used to describe or quantify a chiller's capacity to cool/remove heat.
Capillary Tube
A capillary tube is a very small tube or multiple tubes through which refrigerant is forced in order to reduce the pressure of the liquid in a controlled manner and maintain a desired temperature. The amount by which the pressure is reduced is determined by the length and diameter of the capillary tube.
Cascade
Cascade Chiller Systems combine two separate refrigeration cycles that share one Heat Exchanger. One side of the heat exchanger is used for Evaporating the refrigerant of the First Cycle (High Stage) and the other side to Condense the refrigerant of the Second Cycle (Low Stage). Cascade systems are used in applications in which there is a wide temperature range between the low amd high side, and use two different type of refrigerants which are ideal for their stage and complement each other in the refrigeration process. Essentially, the first stage brings the system's temperature down to a point at which the second stage can rapidly bring the temperature of the Heat Transfer Fluid (and thereby the process) down to Set Point.
Chiller
A Chiller is a machine, piece of equipment or device that circulates liquid (Heat Transfer Fluid) to a process or process stream in order to remove heat from that system, protect the process and facilitate the result. Cooling usually is achieved via a vapor-compression refrigeration cycle in which Heat Transfer Fluid is circulated through a Heat Exchanger in which the refrigerant stream removes the heat from the heat transfer fluid and thereby the process. There are two primary trypes of Chillers: Water Cooled Chillers, in which the heat is rejected via water flow (see Water Cooled Chillers) and Air cooled Chillers, in which a CDA (Clean Dry Air) stream rejects the heat to ambience (see Air Cooled Chillers). Cryogenic Chillers are also now available, in which the removal of Heat from the Heat Transfer Fluid is accomplished via an N2 supplied/filled chamber from which the rejected heat is expelled to ambience via fan systems.
Cold Trap
The cold trap is a device that condenses all vapors in a gaseous stream, with the exception the desired gas(es), into a liquid or solid in order to prevent the contamination of the next step of a process, or to protect a system component (typically Pumps) from contamination and/or damage. Chillers are employed as dedicated Cold Traps in specialized processes such as De-Vulcanization.
Compressor
The Compressor is the central component of a refrigeration system, pumping Refrigerant at the required pressure and in sufficient quantities in order to meet the cooling requirements of the system. The compressor compresses the saturated vapor coming from the evaporator to a high pressure state, resulting in a superheated vapor which is then condensed (rejecting heat from the system) then evaporated, cooling the load.
Condenser
In heat transfer technology, a condenser is a device used to condense a substance from a gaseous state into a liquid one, by cooling it. In Chiller Technology, circulating refrigerant leaves the compressor as saturated vapor in a high pressure state and enters the Condenser Coils where it is cooled, usually by air (or water in water-cooled systems) flowing across the coils, thereby rejecting the heat, which is then transferred to, or beyond, the surrounding environment.
Controller
In Chiller Technology, Controllers (small computer devices usually physically installed as part of the Chiller Unit) are used to control the Chiller's tasks, from simple ramping to and holding a chilled state in a process, to sophisticated programming such as Cycling and Looping with provisions for Multiple Set Points, Ramp, Soak and Window.
Cycle
In Programmed Temperature Control, a Cycle is one set of programmed tasks or events, called Segments. Typical Segments may be devoted to Running to (a) Set Point, Ramp (the amount of time the system takes to reach Set Point), Soak (the amount of time a setpoint is maintained) and Window (the amount of leeway allowed, or degree of accuracy required, above/below the Set Point, in determining whether the system is 'At Temperature). Any Cycle may, additionally, be programmed to 'Loop' or repeat a designated number of times (see 'Loop').
EN 61326
EN 61326 is the European Union’s EMC (Electromagnetic Compatibility) standard, determining EMC Emissions and Immunity requirements for electrical equipment operating from a supply, battery or circuit being measured. EN 61326 governs the design of electrical equipment involved in control, laboratory use, measurement and testing, and is therefore an important resource for Chiller manufacturers wishing to export to European countries.
Enthalpy
Enthalpy is a measurement of the energy in a thermodynamic system; equal to the internal energy of the system (the energy required to create the system) combined with the effects of pressure and volume; that is, the amount of energy required to make room for the system by displacing its environment and establishing its volume and pressure.
Entropy
Entropy is an expression of the disorder, or randomness of a system. In Thermodynamics, and discussions of Absolute Zero, it is a measure of the amount of a system's thermal energy per unit of temperature that is unavailable for accomplishing work.
Evaporator
Evaporator is a term ported over from traditional Mechanical Refrigeration, wherein the refrigerant is evaporated by evaporator coils to cool an area, substance or process. In Chiller Technology, the Evaporation process is generally achieved as part of the heat exchange process; as the refrigerant is evaporated in the Heat Exchanger as the Heat Transfer Fluid is cooled (see Heat Exchanger, below).
Flash Point
Flash Point is the temperature at which the vapors produced from Heat Transfer Fluid (HTF) will ignite (flash off) with the presence of an ignition source; the fluid itself will not burn at this temperature. Flash point is important from the viewpoint of safety, however, it is quite common for heat transfer systems to be operated at temperatures above the flash point of the fluid, as sufficient oxygen and an ignition source are not present in a closed HTF system. The danger lies in leakage, and emphasizes the inportance of regualr checks for leaks in a Chilling System, as external 'weeping' leaks from fixtures can oxidize and produce smoke (though not ignite), and internal leaking of HTF into the porous insulation of the chiller can actually cause the HTF to ignite, as the heat generated by oxidation is trapped in the insulation and can exceed the fluid's auto-ignition temperature.
Flow Rate
In fluid dynamics, the Volumetric Flow Rate, (usually referred to in Chiller systems as the Flow Rate) is the volume of fluid which passes a point per unit of time. The Flow Rate of the Heat Transfer Fluid is one of the parameters (along with Fluid Pressure) that regulates the speed and extent of transfer of heat from the load.
Fluid Bypass Circuit
A Fluid Bypass Circuit is a safety device similar to a Pressure Relief Valve, used in Fluid Systems to control or limit pressure in the system which could otherwise exceed the indicated or set level and result in the interruption of a process, damage to equipment, or a catastrophic event (fire, explosion, etc.). In the case of the Bypass Circuit, however, pressure is relieved as the pressurized fluid is allowed to recirculate in the system rather than continue its normal path until the condition is relieved. The Fluid Bypass Circuit is set or pre-designed to open at a predetermined pressure.
Fluid Chillers
The term Fluid Chiller refers to chillers which use Fluid Heat Transfer Mediums such as Ethylene and Propylene Glycol/Water mixture to carry heat away from the process, to be rejected in the refrigeration cycle of the chiller.
Freezing Point
Freezing point is the temperature below which a liquid turns into a solid. It is necessary to choose fluids, and design and program Chiller Systems, such that the fluids in the sytem do not reach the freezing point.
Gas Chillers
Chillers which use Gaseous Heat Transfer Media such as Argon, Nitrogen Gas and Air to carry heat away from the process, to be rejected in the refrigeration cycle of the chiller.
Glycol (Ethylene Glycol) (Propylene Glycol)
Glycol Chillers use Heat Transfer Fluid with concentrations of Glycol (Ethylene Glycol or Propylene Glycol) to protect the Evaporator and lines from freezing. Glycol Chillers are used in applications that require rapid achievement of very low temperatures or involve the risk of low line loss, slow line flow or pressure drop. Achieving the correct percentage of glycol is key, as a concentration that is too high can cause significant drop in chiller efficiency and capacity. In applications characterized by contamination/toxicity concerns, Propylene Glycol is preferred for its non-toxicity.
Glycol Chiller
Glycol Chillers use Heat Transfer Fluid with concentrations of Glycol (Ethylene Glycol or Propylene Glycol) to protect the Evaporator and lines from freezing. Glycol Chillers are used in applications that require rapid achievement of very low temperatures or involve the risk of low line loss, slow line flow or pressure drop. Achieving the correct percentage of glycol is key, as a concentration that is too high can cause significant drop in chiller efficiency and capacity. In applications characterized by contamination/toxicity concerns, Propylene Glycol is preferred for its non-toxicity.
Heat Exchanger
A Heat Exchanger is a device used to transfer heat between substances, generally for the purpose of removing heat from a process, space or environment. In Chiller technology, the exchange is generally between two fluids, for the purpose of removing heat from a load or product. This process usually involves receiving a liquid vapor refrigerant mixture from the condensing function of the system, and passing it through an arrangement of coils, plates and/or fins wherein the liquid passes close to, and in the opposite direction from, the heat transfer fluid coming from the load, evaporating the liquid part of the cold refrigerant mixture, which cools the transfer fluid which is then returned to the load. The resulting evaporated refrigerant is then moved to the compressor to be recirculated in the process.
Heat Transfer
Heat Transfer is the process of thermal energy moving from one body to another - There are three types of Heat Transfer: Conduction is the transfer of heat from one particle of matter to another, Convection is the transfer of heat from one part of a particle to another by the mixing of the warmer particles with the cooler; and Radiant is the transfer of heat from one body to another as the result of the bodies emitting and absorbing radiation energy. The Heat Transfer in the Heat Exchanger of a typical Chiller is Conductive Transfer.
Heat Transfer Fluids (HTF)
Heat Transfer fluids exchange Heat with Refrigerants (Primary Fluids) to facilitate the removal of heat from a Process/Load. The heat transfer fluid interfaces, through a variety of means, with the load, to remove heat from the load, which is then removed from the heat transfer fluid by the refrigerant using Heat Exchangers (typically composed of touching and/or interlocking Conductive Coils and Heat Transfer Fins). Commonly used in the Chiller Industry include HFE-7100, Ethylene Glycol/Water, Kryo-60, Syltherm and PAO Oil.
Heater
In Chiller Technology, Heaters, of varying types and installation methods, are the means by which, in the chilling process, Temperature is regulated and controlled.
HFE-7100
HFE-7100 is a Heat Transfer Fluid (See Heat Transfer Fluid) commonly used in Chiller Technology. HFE-7100 is a Non-flammable, Low toxicity, Zero Ozone Depletion Potential HTF with a Boiling Range of 50 °C - 99 °C.
IEC 60204
The IEC (International Electrotechnical Commission) is an international organization that prepares and publishes International Standards for all electrical, electronic and related technologies. IEC 60204-1:2016 applies to electrical, electronic and programmable electronic equipment and systems, as well as to machines not portable by hand while working, including groups of machines working together in a coordinated manner, making it very relevant to the design and manufacture of Chiller Systems.
IEEE
IEEE is a grouping of Electrical Standards applicable to the design, manufacture and documentation of state-of-the-art Chiller Equipment. These standards are set out by the Institute of Electrical and Electronics Engineers Standards Association, developed from the consensus of its voting industry-representative and scientific members worldwide.
ISO
ISO is one of the many Industry standards applicable to the design, manufacture and documentation of state-of-the-art Chiller Equipment. ISO 9001:2015 is an internationally recognized document produced and maintained by the International Organization for Standardization, which defines and promotes worldwide proprietary, industrial and commercial standards.
ITAR
The International Traffic in Arms Regulations or 'ITAR', implements the Arms Export Control Act (AECA), which gives the US Department of State oversight and control of the export and temporary import of defense articles and services designated by the Act. Most military development and equipment contracts, including the manufacture of chillers destined to be used in such research and development, are governed by ITAR.
Kryo 60
Kryo 60 is a Silicone-based Heat Transfer Fluid (See Heat Transfer Fluid) commonly used in Chiller Technology. The fluid is a colorless, very low-viscosity (kinematic at 20 °C ) silicone oil for low temperature applications, with an Operating Temperature Range Of -60° to 80 C, and a Fire Point > 110 °C.
LCO2 (Liquid Carbon Dioxide)
Liquid Carbon Dioxide is the Liquid form of Carbon Dioxide Gas; in the Chiller Industry, Liquid Carbon Dioxide is used as a cooling agent.
LN2 (Liquid Nitrogen)
In Chiller technology, LN2 may be utilized to either supplement or replace the traditional Mechanical (Compressor Based) Refrigeration Systems found in most standard chillers.
Load (Heat Load)
Heat Load is a calculated thermal value used to define the amount of cooling power (heat that must be removed) necessary to effectively control the temperature in a defined space in order to meet user requirements. In Chiller technology, the 'Space' is generally a process which is being temperature-controlled.
Looping (Loop)
In Programmed Temperature Control, Looping describes the process of repeating the segments in a Cycle (see Cycle) a designated number of times; each repetition is a 'Loop'.
NFPA 70
Throughout the United States and around the world, NFPA 70/National Electrical Code (NEC), sets the foundation for electrical safety in industrial occupancies, including the design, manufacture and documentation of state-of-the-art Chiller Equipment. The Code presents the latest comprehensive regulations for electrical wiring, overcurrent protection, grounding, and installation of equipment. Adopted in all 50 states, the NEC is the benchmark for safe electrical design, installation, and inspection protecting users and property from electrical hazards.
Noise (Electrical Noise)
Electrical Noise is any undesirable, unwanted electrical interference or disturbance to a given electronic signal. In Chiller Technology, Noise is generally characterized as cyclic or pseudo-random signals coming from other components in the equipmemnt, or from other electronic signal msources in the immediate area. This electrical noise can interfere with the accurate readings necessary for precise temperature programming, generation and control.
Open Loop' and 'Closed Loop' Chillers
The term Closed-Loop Chiller refers to Chillers that are self contained, in that the reservoir, pump, and evaporator are all contained within the chiller, with the coolant continuously recirculating within the unit to remove heat by means of a Heat Transfer Medium. Open Loop Chillers control the temperature of a liquid in a remote open tank (in the case of large Industrial Chillers) or, in the case of Portable Chillers, the temperature of a Process, by continuously recirculating it. The liquid is drawn from the external tank or process, pumped through the Chiller and back to the tank/process. The term Open Loop is also used to refer to cooling systems in which Expendable Cryogenic Coolants such as Liquid Nitrogen (LN2) or Liquid Carbon Dioxide (LCO2) must be periodically replenished by the end user.
Packaged Chiller Systems
Systems in which all the major components of the refrigeration system are located in one integral enclosure. Package configurations are popular for their convenience of installation and use, economy and smaller footprint. Water-cooled and Air-cooled systems are the most commonly 'packaged' chillers. See Split System, below.
PID (Proportional/Integral Derivative)
PID (Proportional/Integral/Derivative) is a Control Loop Feedback mechanism used in applications requiring continuously modulated control for increased accuracy. In Chiller technology, PID is used to maintain the set point as consistently and accurately as possible. The PID controller reads the signal from the Thermocouple/RTD sensor(s) to determine the current process temperature, subtracts that reading from the set point, then applies three predetermined constants working in conjunction with one another to act upon the error and maintain the set point as closely as possible. The Proportional Term (P) adjusts the output proportionally to the error by multiplying the error by a Proportional Gain Constant (Kp). The Integral Term (I) measures the degree and frequency of errors over time, and multiplies this accumulated offset by the Integral Constant (Ki), which represents a 'steady state error' for the process, to remove set point vs measured value errors. The Derivative Term (D) measures the scope/rate/ramp of the error and multiplies it by the Derivative Constant (Kd), which represents the amount of the derivative term that will be applied to the overall control output; predicting the behavior of the system and stabilizing the process accordingly. PID values must be correctly calculated for the particular process, or the process may become unstable and/or slow to respond. Many chillers therefore employ 'autotune' functions, using an 'autotune' period in which the rates and degrees of change, and response times of the process are monitored and used to establish the P, I and D values to be stored and used by the controller.
POA Oil
POA Oil is a Heat Transfer Fluid (See Heat Transfer Fluid) commonly used in Chiller Technology; a highly branched, compact, and extremely stable synthetic hydrocarbon used frequently in military and aerospace applications for its dielectric properties and wide range of operating temperatures. POA Oil offers exceptional heat transfer performance over a wide temperature range and has a thermal conductivity of 0.14 W/m°C. However, although dielectric fluids provide low risk liquid cooling for electronics, they generally have a much lower thermal conductivity than water and most water-based solutions.
Portable Chiller
Portable Chiller refers to any Chiller System that can reasonably moved from one application or location to another, usually by means of built-in Casters, in which all components are contained in a single integral enclosure; as opposed to large tonnage permanent chilling systems which are permanently installed in a fixed location.
Pressure Relief Valve
A Pressure Relief Valve (PRV) is a type of safety valve used in Fluid Systems to control or limit pressure in the system which could otherwise exceed the indicated or set level and result in the interruption of a process, damage to equipment, or a catastrophic event (fire, explosion, etc.). Pressure is relieved by allowing the pressurized fluid to flow from an alternate passage and out of the system. The PRV is set or pre-designed to open at a predetermined pressure.
Process
In engineering, a Process is a series of interrelated tasks that, together, transform inputs into outputs, or result in a finished product. In Chiller Technology, the process is the activity (usually a manufacturing system), from which heat must be removed in order to protect the process and facilitate the result.
Process Cooling
The majority of Chiller applications are designed to, (in a variety of ways depending upon the application), provide temperature control for manufacturing (automotive, energy, chemical processing, industrial, semiconductor) and food/beverage production processes which require low temperature process cooling. Heat transfer fluid is circulated to the process in question, drawing the heat from the process back to the refrigeration cycle of the chiller where the heat is rejected, and the heat transfer fluid returned to the process again.
Pump
A pump is a device that uses reciprocating or rotary mechanisms to move fluids by mechanical action from one location to another, consuming energy to perform the mechanical work of moving the fluid. In Chillers, pumps are used to recirculate Heat Transfer Fluids to facilitate the process of removing heat from a load, and transferring that heat to the refrigerant.
Ramp
Ramp is a term used in temperature generation to describe the amount of time it takes for the system to reach Set Point. This Ramp Speed can be set in the programming of the system to be more or less rapid, according to the needs of the application.
Refrigerant
Refrigerants (Primary Fluids) are used in compression refrigeration cycles that require compression, condensation, expansion and evaporation sequences to phase transition from a liquid to a gas and back again, thereby removing heat from the load. They are direct expansion fluids that evaporate in the portion of the process that requires refrigeration/cooling. Refrigerant types include chlorofluorocarbons and non-halogenated hydrocarbons.
RTD (Resistance Temperature Detector)
Resistance Temperature Detectors (RTD) are Temperature Sensing Probes constructed of finely wound platinum wire in which temperature changes produce corresponding, predictable linear resistance changes; Resistance Increases as the Temperature Rises. RTDs are a common device used in Chillers to obtain the Output and DUT temperatures readings necessary for precise temperature programming, generation and control. RTDs are superior to Thermocouples in that their readings are more accurate, stable, and more repeatable, and receive more robust signals. They are substantially more expensive than Thermocouples, however, leading to a cost vs. accuracy/durability decision when choosing which type of temperature sensing device is appropriate for a particular chiller.
SEMI-S2
SEMI-S2 is a set of performance-based Environmental, Health and Safety (EHS) Standards and Guidelines applicable to equipment used to manufacture, measure, assemble and test Semiconductor Products, including the design, manufacture and documentation of state-of-the-art Chiller Equipment. SEMI-S2 is a product of SEMI, a global Electrical Industry Association, and is developed from the consensus of its voting industry-representative and scientific members worldwide. Related standards are SEMI F47 (Line Drop) and Semi S8 (Ergonomics).
Set Point
The desired temperature, Hot, Cold, or Ambient to which a Temperature Generating Device is programmed to Run (achieve). When the system has reached that Set Point, the System is said to be 'At Temperature'.
Soak
Soak is a term used in temperature generation to describe the amount of time that a set point is maintained before the system moves on to the next segment of a cycle. This Soak Time can be set in the programming of the system to be longer or shorter, according to the needs of the application.
Split Chiller Systems
Systems in which some portion of the chiller's system, such as the condenser, is located remotely, apart from the controller cabinet. Split chiller systems are most commonly used in applications in which the load being chilled must be stored separately, as in the beverage and hospitality industries, or where equipment weight and/or footprint are concerns. Split chiller configurations are most commonly found in the air-cooled category. See Packaged Chiller System, above.
Syltherm
Syltherm XLT and Syltherm 800 are Silicone-based Heat Transfer Fluids (See Heat Transfer Fluid) commonly used in Chiller Technology. They have low fouling potential, a Low Freeze Point, and High Temperature Stability and are Non-Corrosive. They have low acute oral toxicity, and are Non-reportable under SARA Title III. Syltherm XLT has a recommended use range from -101°C to 260°C and is ideal for low temperature heat transfer and promotes pump ability. Syltherm 800 is designed for high temperature liquid-phase operation, and has a recommended operating range of -40°C to 400°C.
Thermal Engine
Thermal Engine is conceptual term which describes the Cooling Capacity of a particular system, typically expressed in a relationship between the amount of Heat Energy in Watts that needs to be removed from the process, and the operating temperature of the system, i.e. 55W at -55°C, 125W at -40°C.
Thermocouple
Thermocouples are temperature sensing probes manufactured of a combination of metal oxides with varying conductive properties, encapsulated in epoxy or glass. Changes in temperature produce proportional changes in resistance, with resistance decreasing as temperature rises. Although RTDs are superior to Thermocouples in accuracy and durability, they are substantially more expensive than Thermocouples, therefore, a cost vs. accuracy/durability consideration is necessssary when choosing which type of temperature sensing device is appropriate for a particular chiller.
Ton (Tonnage)
Tonnage is a way of measuring a particular chiller's ability to cool. A 'ton' of cooling expresses the amount of heat transfer required to melt 1 short ton of pure ice at 0 °C (32 °F) in 24 hours.
UL
UL typically refers to a broad set of Industrial and Scientific Standards, developed by the Safety Science company UL to provide guidelines and certification of industry practices and manufacturing. Many of these standards, particularly Electrical Standards, are applicable to the design, manufacture and documentation of state-of-the-art Chiller Equipment. These standards are developed based on a consensus of UL's voting industry-representative and scientific members worldwide. Two standards particularly applicable to the Chiller Industry is UL/IEC 61010, which governs Safety in Laboratory Test Equipment, and UL1995, which is concerned with Safety in Heating and Cooling Equipment.
Variable Frequency Drive
A variable-frequency drive (VFD) is an adjustable-speed drive used in electro-mechanical drive systems to control AC motor speed and torque by varying motor input frequency and voltage. VFDs are used in Chiller Systems to control Heat Transfer Fluid Pumps and Compressors.
Water Cooled Chiller
Water Cooled Chillers use Water to remove Heat from the system, using Heat Exchangers (typically composed of touching and/or interlocking Conductive Coils and Heat Transfer Fins) to remove the Heat from the condensing Refrigerant and reject the heat to a separate water stream or source such as a Cooling Tower or natural body of water. Generally used for large applications requiring more than two hundred tons of cooling.
Window
Window is a term used in temperature generation to describe the amount of leeway allowed, or degree of accuracy required, above/below the Set Point, in determining whether the system is 'At Temperature'. The 'Window' can be set in the programming of the system to be wider (in °C or °F) or narrower, according to the needs of the application.
You'll just have to wait
We're learning more every day!